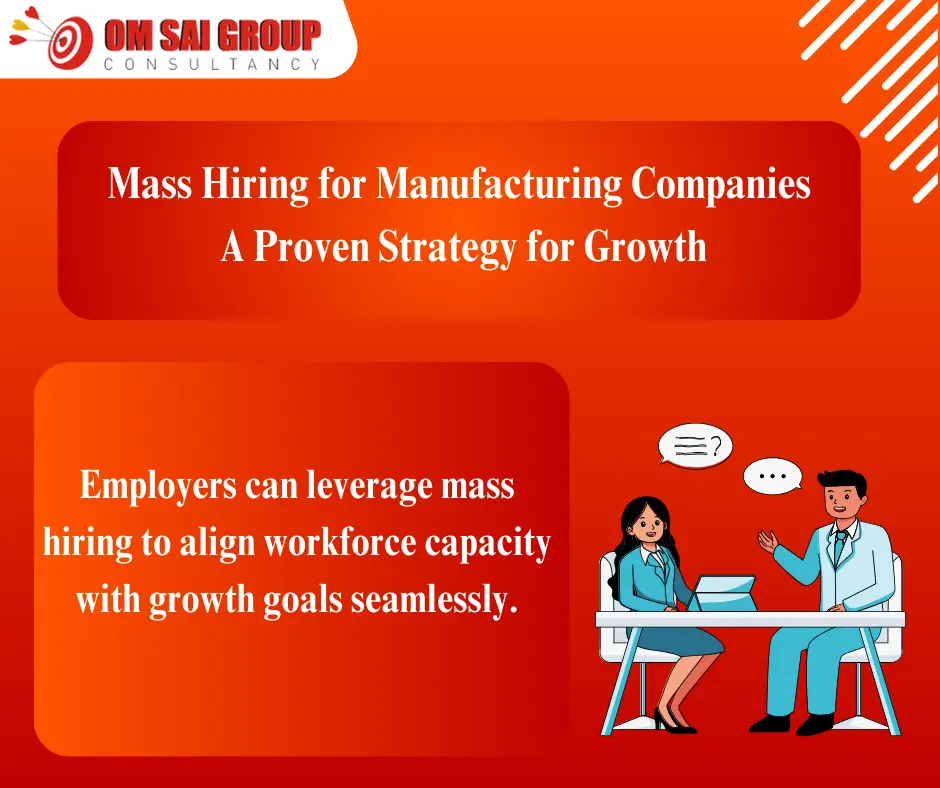
Problem: Understanding the Challenges of Mass Hiring in Manufacturing Companies
Mass hiring is a critical yet complex process for manufacturing companies. Mass hiring for manufacturing companies the global manufacturing sector, which accounted for approximately $44 trillion of GDP in 2022, depends heavily on a reliable and skilled workforce to maintain productivity. However, attracting, screening, and onboarding large numbers of employees come with unique challenges.
Skill Shortage: Manufacturing jobs often require specific technical skills, yet the industry faces a skills gap. According to Deloitte, the U.S. manufacturing sector could have 2.1 million unfilled jobs by 2030.
High Turnover Rates: Manufacturing roles often experience higher turnover rates compared to other industries. The Bureau of Labor Statistics reported an average turnover rate of 37.6% in 2022 for manufacturing companies in the U.S.
Operational Disruptions: Vacant positions can directly impact production timelines, delaying projects and increasing operational costs.
Scaling Difficulties: For companies scaling operations, managing mass recruitment within tight deadlines becomes an overwhelming task, especially during seasonal demand peaks or expansion efforts.
Recognizing these pain points is crucial to creating effective hiring strategies that not only fill vacancies but also contribute to long-term success.
Agitation : The Consequences of Ignoring Effective Mass Hiring Strategies
When companies fail to address the challenges associated with mass hiring, the consequences can ripple across the organization:
Reduced Productivity: Unfilled roles mean production delays, missed deadlines, and frustrated clients. For instance, a large automotive manufacturer reported a 15% decline in output due to understaffing during a critical product launch.
Higher Recruitment Costs: Inefficient hiring processes inflate recruitment expenses. A study by the Society for Human Resource Management (SHRM) estimates that the average cost per hire in manufacturing is $4,425. Scaling this up for mass hiring can strain budgets.
Employee Burnout: Existing employees are often burdened with additional responsibilities when positions remain vacant, leading to decreased morale and higher attrition.
Compromised Quality: Rushed hiring decisions can result in subpar hires, impacting product quality and risking customer dissatisfaction.
Case studies from manufacturing giants highlight the tangible effects of these challenges. For example, a mid-sized electronics firm that underestimated its hiring needs faced a six-month production delay, losing contracts worth $10 million. Ignoring the intricacies of mass hiring is not just risky—it can be disastrous.
Solution : Strategies for Successful Mass Hiring in Manufacturing Companies
To combat these challenges, manufacturing companies must adopt data-driven and efficient hiring strategies. Below are actionable solutions that align with proven case studies and industry best practices:
1. Leverage Technology and Automation
Technology plays a pivotal role in streamlining the hiring process. Tools like Applicant Tracking Systems (ATS) and Artificial Intelligence (AI)-driven platforms can:
Screen Applications: AI can review resumes for required skills and qualifications, reducing manual efforts.
Schedule Interviews: Automated scheduling tools help manage interview slots efficiently.
Provide Insights: Predictive analytics identify candidates likely to succeed in specific roles.
Case Study: A global consumer goods manufacturer used AI-based screening to process 50,000 applications for 5,000 roles in three months. The technology reduced the hiring timeline by 40%, saving $1.2 million in costs.
2. Build a Talent Pipeline
Proactive recruitment ensures that a pool of qualified candidates is ready when needed. Strategies include:
Partnerships with Educational Institutions: Collaborating with trade schools and universities to source skilled talent.
Internal Training Programs: Upskilling existing employees for advanced roles.
Employee Referrals: Encouraging current employees to refer potential hires, which often leads to better cultural fit and lower attrition.
Case Study: A leading aerospace manufacturer implemented a “ready talent” program, creating a database of pre-vetted candidates. This reduced time-to-hire from 60 days to 20 days during a large-scale expansion.
3. Focus on Employer Branding
Manufacturing companies often struggle with perception issues, particularly among younger generations. Highlighting benefits such as competitive pay, career growth opportunities, and a positive work environment can attract talent.
Case Study: A major automotive firm revamped its employer branding, emphasizing innovation and sustainability. This campaign led to a 25% increase in applications within six months.
4. Optimize Onboarding Processes
Efficient onboarding ensures new hires are productive sooner. Key elements include:
Digital Onboarding: Providing online portals for paperwork, training modules, and FAQs.
Buddy Systems: Pairing new hires with experienced employees to ease integration.
Feedback Mechanisms: Regular check-ins during the first 90 days to address concerns and ensure alignment.
Case Study: A machinery manufacturing company reduced new hire attrition by 30% after implementing a structured 90-day onboarding program.
5. Outsource When Necessary
Collaborating with staffing agencies can ease the burden of mass hiring, especially during peak seasons. Agencies provide:
Access to pre-screened talent.
Expertise in niche roles.
Reduced administrative workload.
Case Study: An electronics manufacturer partnered with a staffing agency to fill 2,000 temporary roles during the holiday season. The partnership ensured all positions were filled within six weeks.
6. Adopt Flexible Workforce Models
Flexibility is key to managing demand fluctuations. Options include:
Temporary Workers: Hiring seasonal employees to manage peak periods.
Shift Adjustments: Offering part-time roles or alternate shift patterns to widen the candidate pool.
Case Study: A food processing company increased its shift flexibility, attracting a diverse workforce and reducing staffing gaps by 18%.
Conclusion: Building a Scalable and Sustainable Workforce
Mass hiring in manufacturing companies is no small feat, but it is achievable with the right strategies. By leveraging technology, fostering talent pipelines, and optimizing processes, companies can overcome challenges and build a workforce that drives growth and innovation. Mass hiring for manufacturing companies
The manufacturing industry is evolving rapidly, and so must its approach to hiring. Embracing data-driven methods and prioritizing employee satisfaction will ensure not only operational success but also a competitive edge in the market. Whether you’re managing a small production line or a global manufacturing hub, the principles of effective mass hiring remain the same: plan, adapt, and execute with precision.